冷間鍛造、温間鍛造、熱間鍛造の違い
常温で「鍛造」することを「
冷間鍛造」といいます。 他の鍛造方法として、300℃~850℃で行なう温間鍛造、1100℃~1250℃で行う熱間鍛造があります。
常温下では、変形抵抗が大きく材料と金型の硬度差も少ないため、高度な工程設計能力が必要となりますが、
温間鍛造・熱間鍛造に比べて面粗さ等の仕上がりや精度が高く、組織の状態(ファイバーフロー)が良いものを生産するのに適した製法といえます。
フォーミングマシン‥‥「横型の多段式鍛造機械」
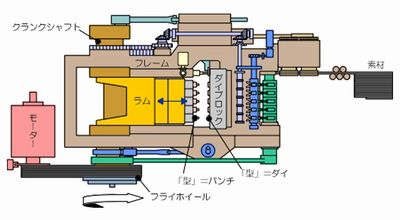
この冷間鍛造を可能にするのがフォーミングマシンです。対向する型(パンチ・ダイス)が複数並び、工程を何段階にも分けて徐々に形状を変えながら完成形状に加工されていきます。
パンチを駆動させるラムは1ストローク約1秒ですので、1秒に1個という圧倒的なスピードで生産を行います。
また、素材から完成形状までの工程を一台のフォーミングマシンで行えるため、中間在庫ができないのもこの製法の大きなメリットといえます。
弊社では主に3段~6段のフォーミングマシンを使用しています。
鍛造と切削の違い ファイバーフロー
木材に木目があるように、鋼材にも組織の流れがあります。
まるで粘土細工のように材料をつぶしたり伸ばしたりしながら形状を変化させていく鍛造により出来上がった製品は、繊維組織(ファイバーフロー)が途切れることなく繋がったまま目的形状へと加工されていきます。
一方で切削は、削ることにより目的の形状へと加工していきますので、容易に製造することができる反面、繊維組織は途中で切れることになります。
木材が木目方向によって強度が異なるように、鋼材も繊維組織が形成されることで、衝撃性、疲労強度に優れた製品が出来上がります。